The role of IoT in predictive maintenance for field service

Author
Mongrov’s Tech Library
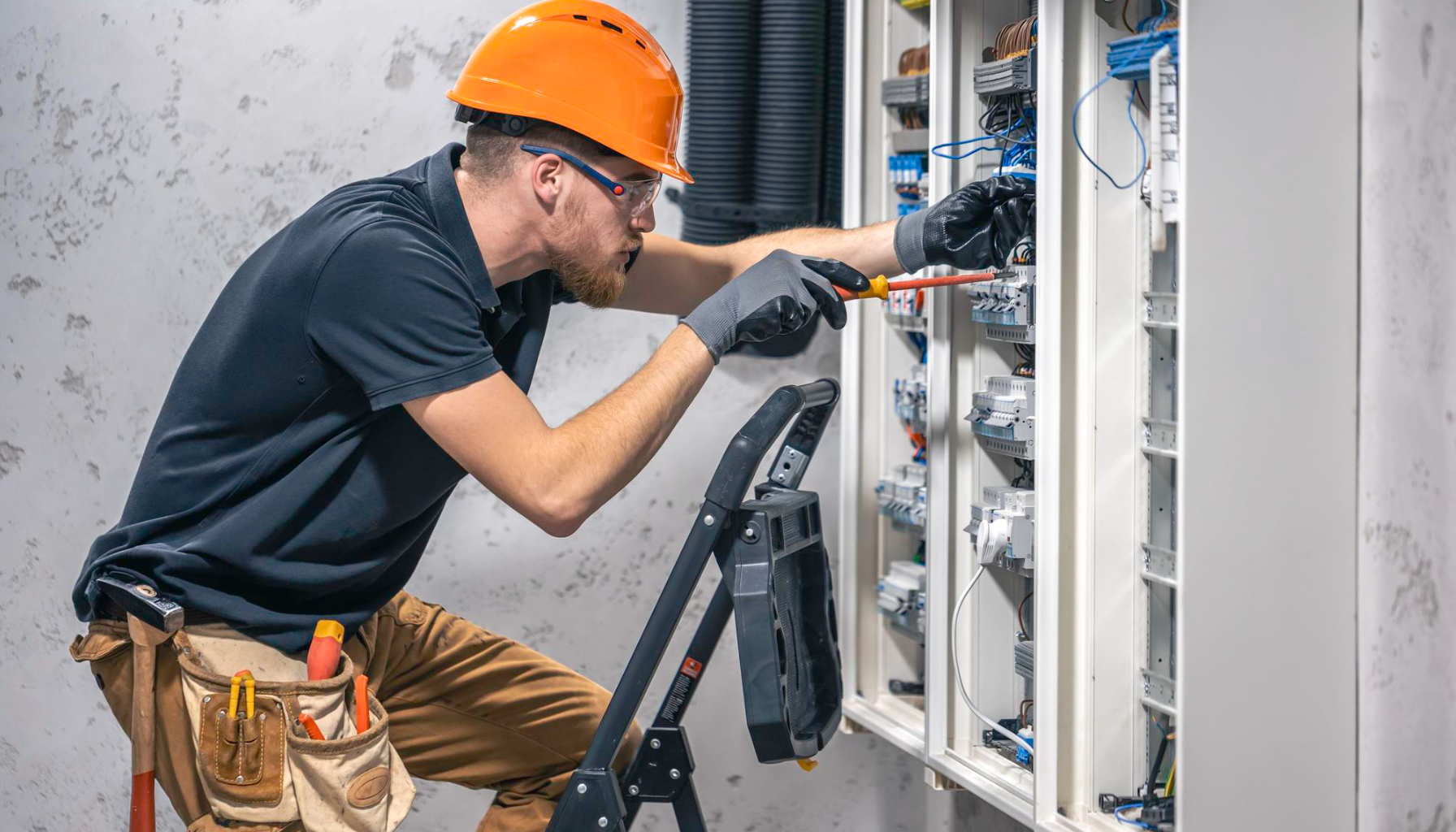
Field service operations are a very significant and vital part of any organization's functioning in the fast-changing world of innovations and businesses. Proper and efficient management of equipment and assets is crucial to lowering downtime and raising production in a variety of settings, including factories, HVAC systems, and more. Nevertheless, reactive initiatives are frequently the foundation of traditional maintenance techniques, which can result in unplanned malfunctions and costly fixes. Predictive maintenance is significantly emerging as an important component of field service management because of IoT.
In this blog, we look at how IoT can impact predictive maintenance in field services, including its benefits, applications, and implementation strategies.
Understanding predictive maintenance and the IoT
By employing machine learning algorithms and data analytics, predictive maintenance is a proactive approach to maintenance that projects the dates of equipment breakdown. Patterns and abnormalities which point towards possible breakdowns can be discovered with predictive maintenance algorithms by examining equipment performance data such as temperature, vibration, and energy usage. Businesses can more likely extend the life of their assets, minimize maintenance expenses, and cut down on downtime by scheduling repairs in advance.
Real-time data collection from sensors and other linked equipment, made feasible by IoT, enables and enhances predictive maintenance. IoT-compatible sensors that are embedded in machinery and gadgets continuously track important performance metrics and provide data for analysis to centralized platforms. Organizations can use massive volumes of sensor data to create predictive maintenance models that identify early warning signals of equipment breakdown and set off maintenance alarms in response by utilizing IoT technologies.
Benefits of IoT in Predictive Maintenance for Field Service
- Reduced Downtime: In making settings, IoT-enabled sensing units keep track of tool efficiency metrics such as temperature level, stress, and resonance, allowing anticipating upkeep to optimize manufacturing effectiveness and lessen downtime.
- Lower Maintenance Costs: By organizing upkeep jobs throughout arranged downtime, anticipating upkeep allows organizations to maximize source application as well as reduce the requirement for costly emergency repair work.
- Extended Asset Lifespan: IoT-enabled anticipating upkeep helps organizations expand the life of their assets and increase return on investment by proactively resolving upkeep problems as well as decreasing funding expenses.
- Improved Safety: Predictive maintenance enhances office security by lowering the probability of mishaps and injuries to device malfunctions by expecting feasible tool failures.
- Optimized Inventory Management: By reducing excess supply as well as boosting supply degrees, anticipating upkeep helps organizations much more properly imagine their requirements for extra components along with stock.
Also Check: The Role of IoT in Asset Security and Theft Prevention
Applications of IoT in Predictive Maintenance for Field Service
Manufacturing
IoT sensors enable machinery to continuously monitor vital performance indicators like vibration, temperature, and pressure in production environments. Through the utilization of this data, predictive maintenance techniques may be smoothly applied to improve production effectiveness and reduce downtime. This integration guarantees continuous productivity and operational excellence in production environments by streamlining operational procedures and encouraging a proactive attitude toward equipment maintenance.
Transportation
IoT sensors in transportation are a smooth integration between vehicles and infrastructure, tracking fuel consumption, tire conditions, and engine functionality with precision. The integration of data enables predictive maintenance systems to forecast and resolve possible problems, hence maintaining the reliability and security of fleet operations. Organizations in the transportation sector may greatly improve fleet safety and reliability standards, guarantee seamless operations, and increase customer satisfaction by proactively addressing maintenance needs based on real-time data insights.
Utilities
IoT sensors work as alert sentinels, closely observing the condition and functionality of equipment within vital utilities such as power plants and water treatment facilities. Predictive maintenance procedures can be put in place to handle seamless service delivery and prevent expensive interruptions by utilizing this data. As protectors, these sensors keep an eye on everything and take preventative measures to protect vital infrastructure while maintaining uninterrupted operations. IoT therefore strengthens the foundation of important utilities that are necessary for modern living, fortifying reliability while also improving efficiency.
Healthcare
IoT-enabled medical equipment and devices act as watchful parents in healthcare environments, monitoring patient welfare and usage habits. In addition to protecting patient health, these extensive monitoring capabilities enable predictive maintenance schedules. Healthcare institutions can maintain the availability and dependability of vital medical assets by proactively evaluating the performance of their equipment. By combining IoT technology with healthcare knowledge, organizations can guarantee continuous care delivery, improving patient outcomes and operational effectiveness.
Must Read: Safety of remote workers: Bringing universal connectivity with IoT
Implementation strategies for IoT-enabled Predictive Maintenance
- Data Collection: Deploy IoT sensing units to accumulate real-time information on tool efficiency metrics such as temperature level, resonance, and power intake.
- Data Analysis: Utilize advanced analytics coupled with artificial intelligence formulas to examine sensing unit information and recognize patterns as a measure of possible device failures.
- Predictive Models: Develop anticipating upkeep designs that take advantage of sensing unit information to project device failings as well as activating upkeep informs based upon predefined limits.
- Integration: Integrate anticipating upkeep systems with existing field service management software programs as well as upkeep processes to enhance procedures and assist in aggressive upkeep preparation.
- Continuous Improvement: Continuously check together with improve anticipating upkeep versions based upon feedback from field service technicians as well as device efficiency information, making sure ideal efficiency plus precision.
Increasing Productivity and Dependability: IoT Predictive Maintenance's Role in Field Service Future
IoT-based predictive maintenance allows companies to efficiently detect and manage equipment-based problems before they persist, representing a dramatic shift in field service management. By using IoT technology in order to gather real-time data from sensors and connected devices, organizations should plan predictive maintenance models that improve maintenance schedules, minimize downtime, and extend asset life. Predictive maintenance has varied uses for IoT, ranging from factories to transportation equipment and more. These applications help businesses operate more efficiently, save maintenance expenses, and guarantee the dependability and security of their assets.
As the IoT evolves, the role of proactive maintenance in field service management will become more critical, driving innovation and efficiency in industries worldwide.