Optimizing Manufacturing Field Services with Predictive Maintenance and IoT

Author
Mongrov’s Tech Library
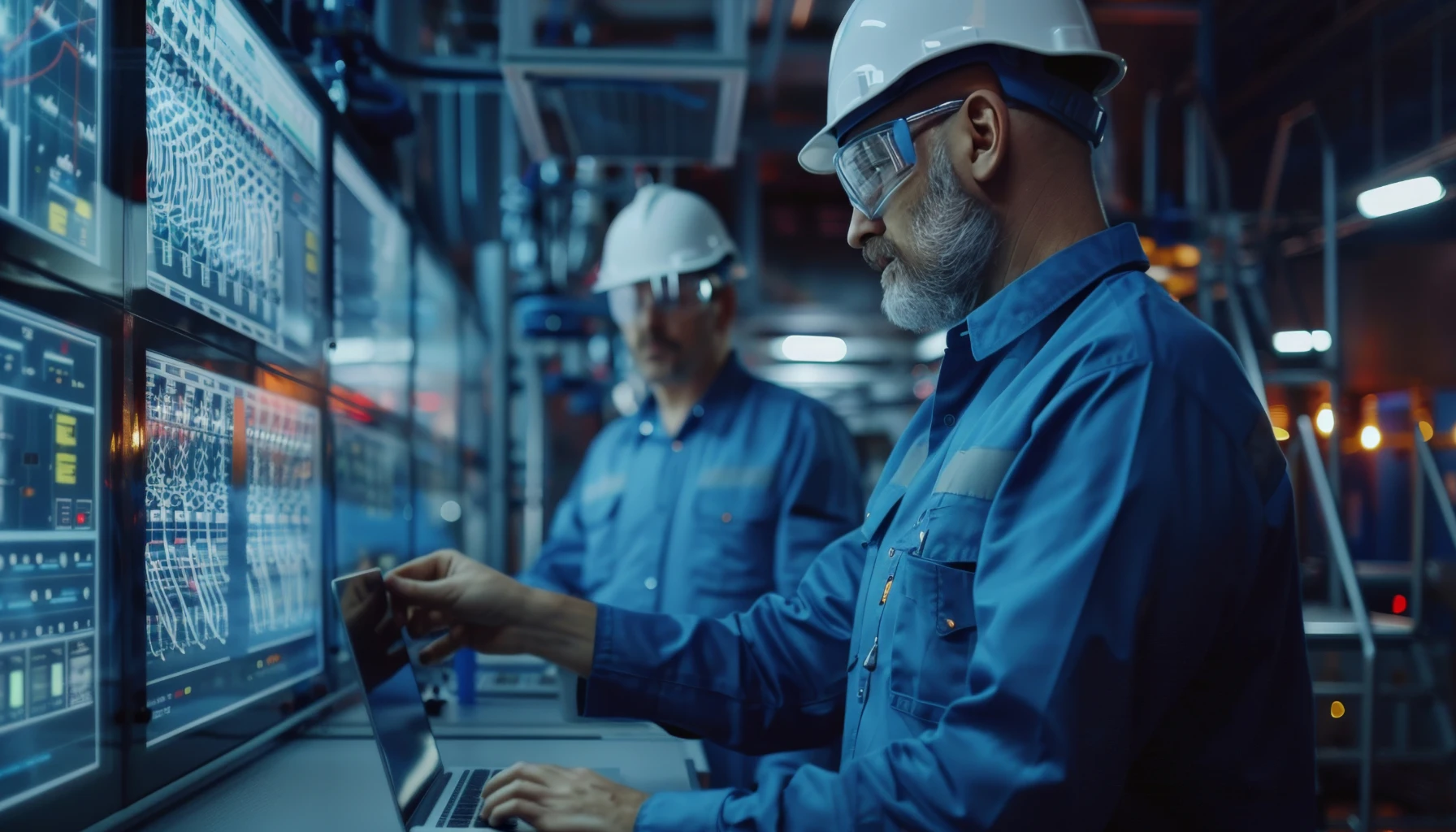
Increased production processes characterize the modern world, where productivity and minimizing lost time are critical. Asset control has changed when looking at IoT products and using predictive preservation. It is anticipated that the market for Internet-of-things production will expand at a compound annual growth rate (CAGR) of 11%. Nine percent, starting at fifty dollars. From 2021 to 2026, the United States dollar price accelerated from 50 billion to 87.9 billion.
The following blog explores approaches to production enhancement using predictive maintenance enabled by IoT field service software.
While IoT and predictive maintenance improve industrial field services, figuring out how IoT sensors identify problems is the next critical step to guaranteeing even higher operational efficiency.
IoT Sensors' Function in Identifying Abnormalities
1. Early identification of malfunctioning equipment
IoT sensors use pressure, vibration, and temperature monitoring to spot irregularities in manufacturing equipment. By doing so, they can avert major problems and guarantee timely repair. General Electric (GE) is a prime example of a company utilizing IoT for predictive maintenance. On its wind turbines, GE placed sensors to collect performance data continuously.
After that, real-time analysis of this data using machine learning techniques allowed for the predicting of when a wind turbine was likely to fail. This reduced downtime and increased output since GE could do maintenance before the wind turbine broke.
2. Monitoring Infrastructure to Improve Safety
IoT sensors are useful for monitoring manufacturing facilities' infrastructure in addition to their equipment. They can identify environmental elements like humidity and air quality as well as structural problems like foundation or wall fissures. By preventing accidents and expensive repairs, this thorough monitoring makes sure that the industrial environment is safe and complies with standards.
IoT sensors are great at finding anomalies, but predictive maintenance uses this information to foresee problems before they affect output, which increases factory efficiency.
Predictive Maintenance's Advantages for Manufacturing
Minimizing Expensive Downtime
IoT data-driven predictive maintenance drastically lowers unscheduled downtime. Planned maintenance or reactive repairs for failing equipment are often the foundation of conventional maintenance approaches. Conversely, predictive maintenance makes use of advanced algorithms and real-time data to predict when equipment is likely to break. Manufacturing operations can be reduced by being proactive and enabling timely interventions.
Increasing the efficiency and uptime of assets
Another important advantage of predictive maintenance in production is increased asset uptime. Manufacturers can maintain manufacturing strains by scheduling upkeep throughout off-height hours and exactly watching for when gadgets might require preservation. By extending the lifespan of devices and enhancing asset efficiency, this optimization of maintenance schedules lowers the need for frequent replacements.
According to research, there will be 267 million asset trackers globally by 2027.
IoT-powered field service software improves production by offering real-time insights and more intelligent operational adjustments for optimal performance, building on the advantages of predictive maintenance.
Using Internet of Things-Powered Field Service Software to Transform Manufacturing Operations
Simplifying Field Service Administration
The Internet of Things (IoT)-powered field service management software enhances maintenance by providing experts with real-time data for precise diagnosis and fixes. Additionally, it guarantees easy communication, keeping everyone informed, between the office and the field. Primarily based on those tendencies, it's widely predicted that by the end of 2023, there will be more than 43 billion net factors devices all over the world, and this is anticipated to have a huge impact on the financial system by 2025.
Building on the Internet of Things' revolutionary potential in the manufacturing sector, let's examine actual cases where this technology is generating noteworthy operational breakthroughs and developments.
Examples of IoT Integration in the Real World
The beverage company Coca-Cola is a great example of another company utilizing IoT for quality control. Coca-Cola installed sensors on its manufacturing line so that it could show the products' niceness in real-time. The sensors' collected data on temperature, pressure, and other parameters was evaluated using system learning techniques.
As a result, Coca-Cola was able to identify anomalies in real-time and take corrective action before they got worse, which reduced the likelihood of producing faulty products and increased customer satisfaction.
Increasing satisfaction with customers
By guaranteeing prompt and effective service delivery, field service software driven by IoT technology also improves client happiness. By employing predictive maintenance data to prevent equipment breakdowns and minimize downtime, manufacturers can better serve their customers. This proactive strategy enhances client relationships and fosters trust, which eventually propels corporate expansion.
Increasing customer happiness is still a top objective, but overcoming obstacles in IoT and predictive maintenance creates new difficulties that need to be resolved to ensure success moving forward.
Overcoming Obstacles in the Application of IoT and Predictive Maintenance
Privacy and Data Security Issues
Factor protection and privacy are important limitations to the economic use of IoT and predictive upkeep. Thinking about the amount of information being accumulated and sent, it's essential to ensure that it is safe from internet assaults. To defend touchy records, producers need to invest in robust cybersecurity solutions and comply with statistics protection regulations.
Controlling the shift to preventive maintenance
Transferring from predictive maintenance to even regular methods of maintenance may require some effort. It takes dedication to the processes of learning and adaptation in addition to a modification of culture in business. The potential benefits of this revolutionary technology and efficient implementation of such a system can be utilized by staff training in the field of IoT and predictive maintenance.
Investigating how these technologies will influence manufacturing in the future and spur innovation is essential as we handle the current IoT and predictive maintenance difficulties.
Prospects for Predictive Maintenance and IoT in Manufacturing in the Future
Developments in machine learning and AI
Manufacturing predictive upkeep will change due to advances in AI and machine-gaining knowledge. With the assistance of this technology, which analyzes massive amounts of data to perceive styles that human analysts regularly pass over, correct failure forecasts and preservation insights might be viable.
Predictive maintenance is predicted to develop rapidly internationally, from $5.7 billion in 2024 to over $39 billion through 2032, in line with current predictions. The Internet of Things is accountable for this notable growth, which is anticipated to grow at a compound annual increase price (CAGR) of 27.1% between 2023 and 2032.
Increasing Use of IoT-Capable Devices
IoT device usage in manufacturing is expected to increase significantly. Lowering sensor costs will make adoption more widely possible, improving data gathering and processing. The expansion of this will increase operational efficiency and predictive maintenance in all of the facilities.
There were approximately 14.4 billion IoT devices in use in 2023, according to reports, as the technology continued to grow quickly. Analysis indicates that there will probably be more than 29 billion IoT connections by 2027.
Integration with Big Data and Advanced Analytics
Manufacturers can have new opportunities when predictive protection, IoT, massive facts, and advanced analytics are integrated. Producers may also make record-driven choices, find areas for development, and reap deeper insights into their operations by making use of large data analytics. The overall effectiveness and competitiveness of producing operations can be stepped forward with the aid of this all-encompassing approach.
As we envision the future of manufacturing, integrating IoT and predictive maintenance will be pivotal in shaping industry advancements and driving operational excellence.
Conclusion: Embracing IoT and Predictive Maintenance as the Future of Manufacturing
In the end, there are some benefits to combining IoT and predictive renovation in manufacturing, such as lower downtime and accelerated productivity. IoT sensors enable proactive maintenance by identifying problems with the equipment.Mongrov, an IoT-powered field service software, improves client happiness and operations. Adopting these technologies is crucial to succeeding in the changing manufacturing sector and maintaining competitiveness.